Imagine a world where every process runs flawlessly, every product meets the highest quality standards, and every customer is completely satisfied. This isn’t just a fantasy; it’s the promise of Six Sigma, a powerful methodology designed to eliminate defects and optimize processes. But how does it work? Enter DMAIC, the acronym that stands for Define, Measure, Analyze, Improve, and Control – the five steps that form the backbone of Six Sigma implementation.

Image: www.babezdoor.com
In my own personal experience, I witnessed the transformative power of DMAIC firsthand when working on a project to streamline the production process at a manufacturing facility. By meticulously following the DMAIC steps, we identified and eliminated a bottleneck causing delays and reduced waste, leading to significant cost savings and increased customer satisfaction. DMAIC proved to be an invaluable tool in driving continuous improvement and achieving operational excellence.
The DMAIC Framework
DMAIC is a structured methodology that provides a step-by-step roadmap for tackling complex problems and enhancing business processes. It’s a data-driven approach that focuses on identifying root causes, implementing solutions, and establishing robust control mechanisms to maintain the improvements achieved.
Each phase of the DMAIC process has specific objectives and tools to achieve them. Here’s a breakdown of each stage:
1. Define: Identify the Problem and Goals
The Define stage sets the foundation for the entire DMAIC project. This involves:
- Defining the problem: Clearly articulate the issue you are targeting for improvement. This includes defining the scope, the impact of the problem, and the desired outcome.
- Identifying the customer: Understanding the customer’s needs helps in defining clear goals and measurable objectives. Conducting customer surveys, analyzing complaints, and gathering feedback are crucial steps in this phase.
- Project charter development: A project charter outlines the problem statement, goals, scope, timeline, and resources allocated to the project.
2. Measure: Gather Data and Establish Baselines
The Measure phase involves collecting accurate data to understand the current process and establish baselines for comparison. This step is critical for:
- Understanding the current process: Mapping the process flow helps identify potential areas for improvement.
- Collecting relevant data: Gathering data on key performance indicators (KPIs) provides a clear picture of the process’s current performance.
- Establishing baselines: Baselines serve as a benchmark for measuring the effectiveness of improvements made in subsequent phases.
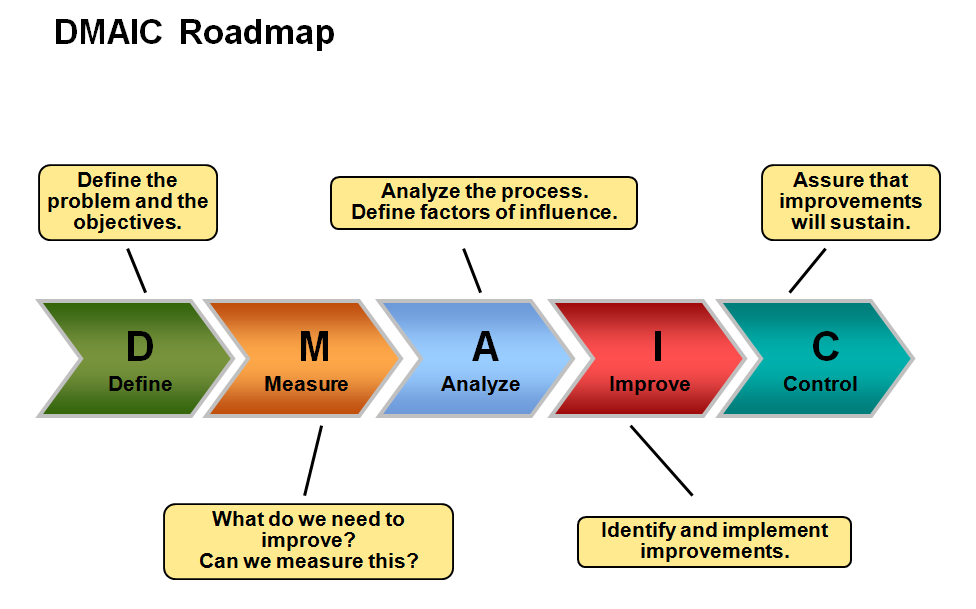
Image: vichemean-softskills.weebly.com
3. Analyze: Identify Root Causes
This is where analytical tools and techniques come into play. The Analyze phase aims to uncover the underlying causes behind the identified problem. It typically involves:
- Data analysis: Statistical tools such as Pareto charts, histograms, and scatter diagrams are used to analyze data and identify patterns.
- Root cause analysis: Techniques like fishbone diagrams and 5 Whys are employed to drill down to the root cause of the problem.
- Prioritization: By analyzing the root causes, the team prioritizes the most impactful ones that require immediate attention.
4. Improve: Develop and Implement Solutions
The Improve phase is where creativity and innovation come into play. Based on the analysis, the team develops and implements solutions to address the root causes identified. This might involve:
- Brainstorming potential solutions: Encourage team members to come up with innovative solutions that address the core issues identified in the Analyze phase.
- Designing and prototyping solutions: Develop prototypes or pilot projects to test the feasibility and effectiveness of potential solutions.
- Implementing the solution: Once a solution is validated, implement it across the process. Ensure proper training and communication for seamless execution.
5. Control: Sustaining the Improvements
The Control phase ensures that the improvements made are sustained over time. It involves:
- Monitoring performance: Continuously track KPIs to monitor the effectiveness of the implemented solutions and identify any potential deviations.
- Developing control plans: Establish control plans that outline procedures, standards, and measures to maintain the process at the desired level of performance.
- Periodic reviews: Conduct regular reviews to assess the effectiveness of the control plan and adjust it as needed.
DMAIC in Action: Real-World Applications
The DMAIC approach has been successfully implemented across diverse industries and sectors. Here are some examples of how companies are leveraging DMAIC to achieve significant improvements:
- Manufacturing: Reducing defects, improving yield, and optimizing production lines.
- Healthcare: Streamlining patient flow, enhancing patient safety, and reducing medical errors.
- Finance: Improving customer service, automating processes, and reducing fraud.
- IT: Reducing downtime, resolving IT issues faster, and improving customer satisfaction.
Tips for Effective DMAIC Implementation
While the DMAIC framework provides a structured approach, successful implementation requires careful planning and execution. Here are some actionable tips to maximize the benefits of DMAIC:
- Strong Leadership: Secure buy-in from top management and ensure they actively champion the initiative.
- Cross-Functional Teams: Assemble diverse teams with expertise from different departments to foster collaboration and generate comprehensive solutions.
- Data-Driven Decision Making: Emphasize data analysis and use it to guide every step of the DMAIC process for objectivity and effectiveness.
- Continuous Improvement Mindset: Encourage a culture of continuous improvement where team members proactively identify opportunities for enhancement.
- Regular Communication and Feedback: Maintain open communication throughout the project. Regularly share progress updates, and solicit feedback from team members to ensure engagement and address any challenges promptly.
Expert Advice for Implementing DMAIC
Based on my experience, I’d recommend the following expert advice:
Start small – Don’t try to tackle too many problems at once. Begin with a focused project to demonstrate the effectiveness of DMAIC and build momentum.
Don’t be afraid to change course – If the initial solution doesn’t yield the desired results, be flexible and adapt your approach. The DMAIC process is iterative, so be prepared to make adjustments based on data and feedback.
FAQs on DMAIC
Q: Does DMAIC apply only to large organizations?
A: DMAIC can be used by organizations of all sizes. Even small businesses can leverage DMAIC to improve efficiency, reduce waste, and enhance customer satisfaction.
Q: How long does a DMAIC project typically take?
A: The duration of a DMAIC project depends on the complexity of the problem and the resources available. However, a typical DMAIC project can range from a few weeks to several months.
Q: What are some common challenges in implementing DMAIC?
A: Challenges include securing leadership buy-in, acquiring accurate data, and fostering collaboration among cross-functional teams.
Q: What are some popular software tools for DMAIC projects?
A: There are many software tools designed to assist with DMAIC projects, including Minitab, JMP, and Tableau. These tools can help with data analysis, visualization, and process mapping.
Six Sigma Dmaic Approach Can Be Used For
Conclusion
The Six Sigma DMAIC approach is a powerful methodology for achieving operational excellence and boosting efficiency. By embracing data analysis, continuous improvement, and a collaborative spirit, organizations can overcome challenges, drive innovation, and deliver exceptional customer experiences. As you move forward on your own continuous improvement journey, I encourage you to explore the powerful possibilities of DMAIC and its potential to transform your organization.
Are you interested in learning more about the DMAIC approach and its applications in your industry?