In the fast-paced world of business, we’re constantly striving for more – more output, less waste, and ultimately, greater profitability. I remember when I first started out, I was overwhelmed by the sheer volume of tasks and processes, struggling to see the big picture. It felt like I was navigating a tangled web with no clear path to success. Then, I discovered value stream mapping – a powerful tool that helped me visualize the flow of work and identify opportunities for improvement. It was a game-changer, and I knew I had to share this knowledge with others.
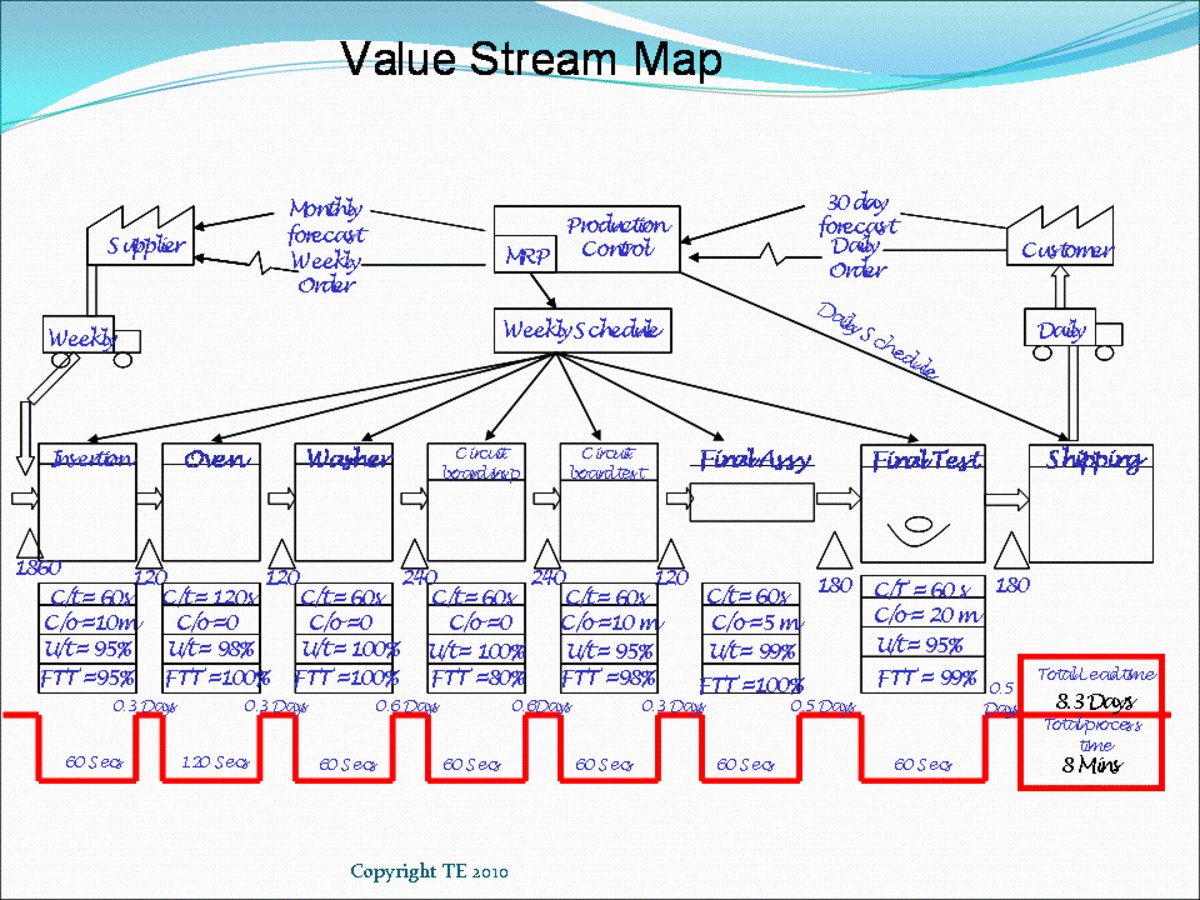
Image: discover.hubpages.com
Through this guide, I’ll take you on a journey through the world of value stream mapping, offering a practical and insightful approach with a downloadable PDF resource. We’ll delve deep into the intricacies of this lean methodology, exploring its applications, benefits, and step-by-step implementation. By the end of this article, you’ll be armed with the knowledge and tools necessary to unleash the hidden potential within your own processes.
Understanding the Power of Value Stream Mapping
Unveiling the Flow: A Visual Representation of Value Creation
Imagine your business as a river flowing from its source to the ocean. Along the way, there are various obstacles – bottlenecks, delays, and inefficiencies that hinder the smooth flow of water. Value stream mapping is like a detailed map of this river, outlining every twist and turn, revealing hidden obstacles, and providing insights on how to optimize its course. It’s a visual representation of all the steps involved in creating value for your customers, from the initial request to the final delivery.
By meticulously mapping out the value stream, we can identify areas of waste, pinpoint bottlenecks, and understand how different processes interrelate. This visual approach provides a shared understanding of the entire workflow, allowing teams to collaborate effectively and make data-driven decisions for improvement.
Delving into the Fundamentals of Value Stream Mapping
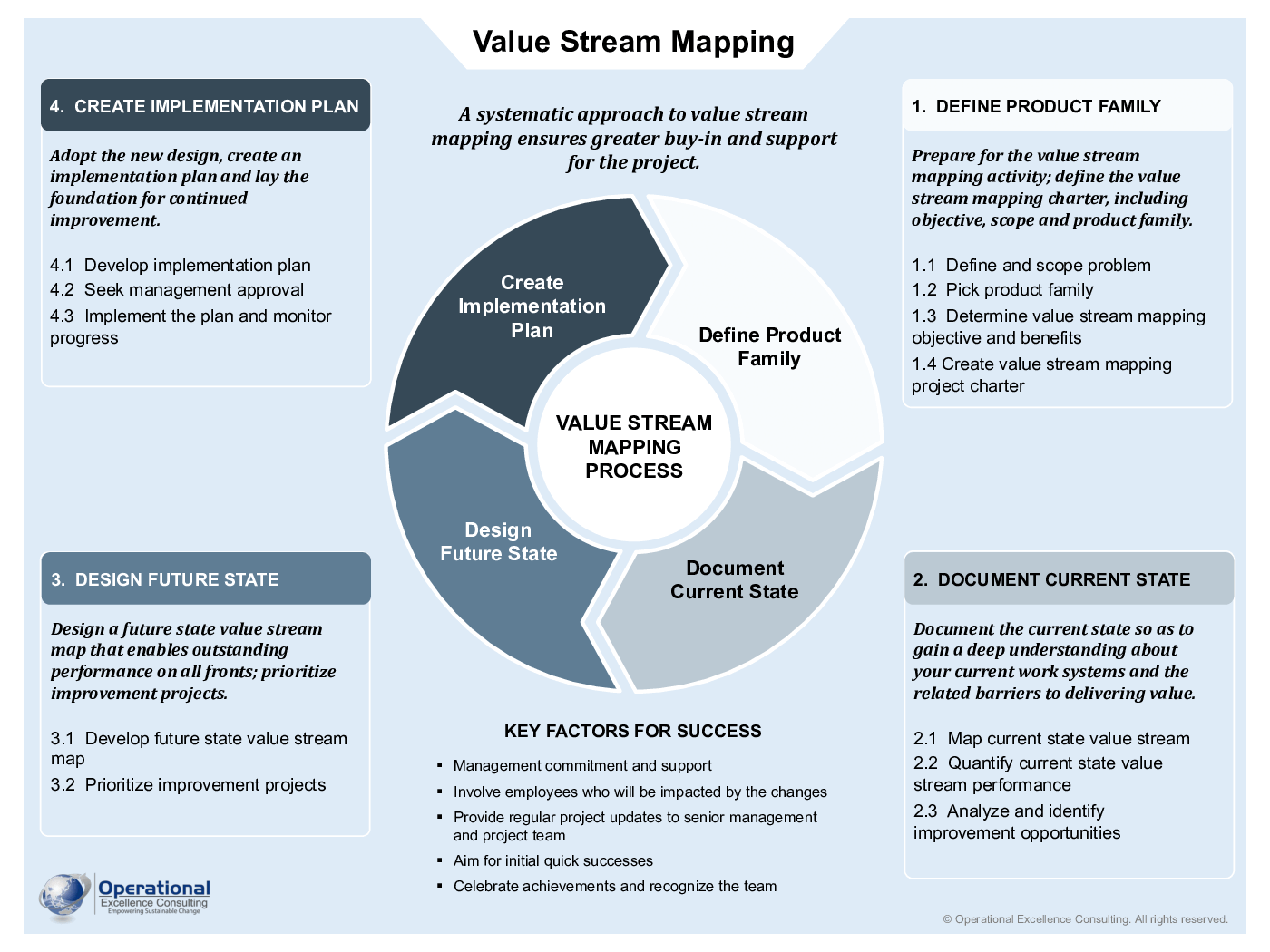
Image: flevy.com
Definition and Origins
Value stream mapping is a lean management technique used to visualize the steps involved in delivering a product or service to the customer. It originated in the Toyota Production System (TPS), where it was instrumental in driving efficiency and eliminating waste. Today, it’s widely adopted across various industries, from manufacturing to healthcare.
The Essence of Value Stream Mapping: Identifying and Eliminating Waste
The core principle of value stream mapping lies in identifying and eliminating waste within a process. Waste, in this context, refers to any activity that doesn’t add value for the customer. It can manifest in various forms, including:
- Overproduction: Producing more than what is needed
- Inventory: Excess materials or parts in storage
- Defects: Errors that require rework or scrap
- Motion: Unnecessary movement of people or materials
- Waiting: Delay in the flow of work due to bottlenecks
- Transportation: Moving materials or products unnecessarily
- Overprocessing: Performing more work than required
By identifying these sources of waste, value stream mapping empowers organizations to streamline their processes, reduce costs, and improve customer satisfaction.
The Essential Steps of Value Stream Mapping
Step 1: Define the Scope of Your Value Stream
Begin by clearly defining the specific product or service you want to map. Determine the start and end points of your value stream, encompassing all the steps from customer request to final delivery. This clarity ensures that you’re focusing on the right area of your business.
Step 2: Map the Current State
The next step involves mapping the current state of your value stream, documenting every step involved in the process. This includes:
- Identifying each process: What are the individual steps involved in creating value?
- Measuring cycle time: How long does it take to complete each process?
- Identifying bottlenecks: Where are the delays and points of congestion?
- Pinpointing sources of waste: Which activities don’t add value for the customer?
This detailed mapping allows you to visualize the current flow of work, highlighting areas that require improvement.
Step 3: Develop a Future State Map
With a clear understanding of your current state, you can now work towards a more efficient future state. This involves:
- Identifying opportunities for improvement: Based on the insights from the current state map, identify potential areas for streamlining, eliminating waste, and reducing cycle time.
- Developing a new workflow: Reimagine your processes, eliminating redundant steps, and optimizing the flow of work.
- Prioritizing improvements: Determine which improvements to implement first, based on their potential impact and feasibility.
This future state map becomes your roadmap for improving your value stream, guiding your implementation efforts.
Step 4: Implement and Communicate Your Changes
Armed with your future state map, the next step is to implement the recommended improvements. This involves:
- Making adjustments to your processes: Put the improvements into action, eliminating waste and streamlining workflow.
- Monitoring and measuring results: Regularly track the impact of your changes on key metrics like cycle time, lead time, and waste reduction.
- Communicating your progress: Share the results of your value stream mapping efforts with stakeholders, ensuring everyone is aligned and informed.
Continuous improvement is key to realizing the full potential of value stream mapping. By implementing and monitoring your changes, you can continuously refine your processes and achieve greater efficiency.
Navigating the Latest Trends in Value Stream Mapping
The Rise of Digital Value Stream Mapping
As technology advances, digital tools are increasingly being integrated into value stream mapping, enabling greater precision and collaboration. Digital value stream mapping solutions offer:
- Real-time data visualization: Visualize your value stream in real time, allowing for dynamic adjustments and continuous monitoring.
- Automated data collection and analysis: Collect and analyze data automatically, reducing manual effort and ensuring accuracy.
- Improved collaboration: Work on the map collaboratively, enabling team members to contribute from anywhere.
These technological advancements are streamlining value stream mapping processes, making them more accessible and powerful.
Embracing Lean Thinking for Sustainable Improvement
Value stream mapping is a core element of lean thinking, a philosophy that emphasizes continuous improvement and waste reduction through a customer-centric approach. Combining value stream mapping with other lean tools like Kanban, 5S, and Kaizen can create a comprehensive system for driving efficiency and excellence within your organization.
Expert Tips for Leveraging Value Stream Mapping
Based on my experience, here are some key tips for leveraging value stream mapping effectively:
- Involve everyone in the process: From frontline workers to management, engage all stakeholders to gain valuable insights and build buy-in for improvement initiatives.
- Start small and iterate: Don’t try to tackle everything at once. Begin with a specific area or process and build upon your success.
- Use the right tools: Leverage digital tools and templates to streamline the mapping process and facilitate collaboration.
- Focus on customer value: Remember that the ultimate goal is to create value for your customers. Always keep their needs at the forefront of your improvement efforts.
By following these tips, you can ensure that your value stream mapping efforts are effective and sustainable, leading to lasting improvements in your operations.
FAQ: Common Questions About Value Stream Mapping
Q: What are the benefits of value stream mapping?
A: Value stream mapping offers numerous benefits, including:
- Increased efficiency: Streamlining processes and eliminating waste leads to faster delivery times and reduced cycle time.
- Reduced costs: Identifying and eliminating waste minimizes unnecessary expenses, resulting in cost savings.
- Improved quality: Focusing on value creation and eliminating defects leads to higher quality products or services.
- Enhanced customer satisfaction: Delivering value faster and with fewer errors results in a positive customer experience and increased satisfaction.
- Improved communication: Visualizing the flow of work creates a shared understanding and promotes collaboration among teams.
Q: Can value stream mapping be used in any industry?
A: Yes, value stream mapping is a versatile tool that can be used in virtually any industry – manufacturing, healthcare, software development, finance, and more. The principles are universal, applicable to any process involving the creation and delivery of a product or service.
Q: What are some common mistakes to avoid when value stream mapping?
A: It’s important to avoid common pitfalls, such as:
- Not involving the right people: Ensure you have input from all relevant stakeholders, including frontline workers and managers.
- Overcomplicating the map: Keep your map visually clear and concise, focusing on the essential steps and avoiding unnecessary details.
- Not measuring results: Track the impact of your changes on key metrics to ensure improvement and ROI.
- Not making it a continuous process: Value stream mapping should be an ongoing effort, continuously refining processes and adapting to evolving needs.
Learning To See Value Stream Mapping Pdf
Embracing the Power of Visualization for Continuous Improvement
In conclusion, value stream mapping is a powerful tool for unlocking hidden potential within your operations. By visualizing your processes, identifying waste, and implementing continuous improvement initiatives, you can transform your business, achieve greater efficiency, and deliver exceptional customer experiences. This guide has taken you on a journey through the world of value stream mapping, equipping you with the knowledge and tools to embark on your own journey of optimization and success. Are you ready to unlock the efficiency hidden within your processes?
If you’re interested in diving deeper into value stream mapping or exploring other lean methodologies, please don’t hesitate to share your thoughts and questions! I’m always happy to connect and learn from others on this journey of continuous improvement.